Junior Factory Manager - Vereeniging, South Africa - Victoria Devereux International
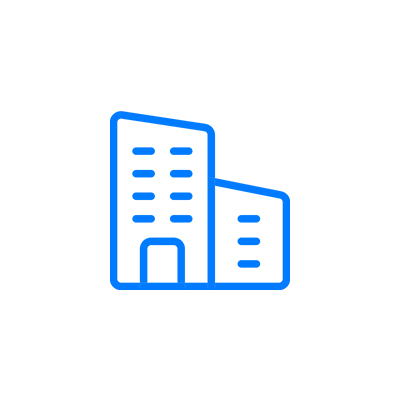
2 weeks ago
Description
Level of Work:
Middle Management
Direct report (solid line):Factory Manager
Sponsor:
Chief Executive Officer
Minimum Education required:
NQF Level 6/7 Degree in an Engineering discipline - Mechanical, Electrical, Chemical or Metallurgy
Qualification in financial management is advantageous.
Minimum Experience required: 1-3 years post qualification engineering or process experience in FMCG or mining industry.
Purpose of the Role:
The main responsibility of the Junior factory manager is to acquire all essential knowledge and skills to become a future Factory manager.
The Junior factory manager is responsible to support the Factory manager to manage all aspects of running the business to achieve the desired growth, profit and strategic business objectives or ambitions of the business unit.
Primary Responsibilities
Task & responsibilities
Development of asset preservation strategy
- Assist in the development of the asset preservation strategy, AM objectives and operational plans.
Implementation of asset preservation strategy
- Translate the asset preservation strategy and AM objectives into plans, budgets and KPIs for the maintenance function and assist in identifying the resources to execute these plans.
- Allocate budgets and performance targets to relevant heads of department.
Management of Maintenance effectiveness
- Oversee the effective execution of preventive and reactive maintenance work in the allocated department or section to optimise their performance at mínimal cost and risks.
- Review the work orders stats for the allocated department or section (Work order status; backlog; schedule compliance; performance) and address any problems with relevant heads of department.
- Monitor the cost of maintenance for the allocated department or section (SAP & Excel maintenance sheet) and highlight any problems with relevant heads of department.
- Evaluate and manage critical plant/equipment status for assets within the allocated department or section to determine when to schedule a planned maintenance stop.
Drive quality and eliminate defects through continuous improvement.
- Drive continuous improvements within the allocated department or section for process and maintenance (KPI review meetings; defect elimination; small project; recognition).
- Develop and combine all continuous improvement tasks/opportunities for allocated department or section.
- Identify resource to allocate projects and tasks.
- Ensures the master tile specifications are kept valid.
- Investigate customer complaint to understand the defect, its causes and implement measures to prevent reoccurrence.
- Report on progress and status of all customers complaints.
- Monitor labs stats on product specification to identify project opportunities.
- Identify issues in inefficiency and suggest improvements.
Lead, Manage and direct People.
- Manage and lead departments heads.
- Facilitate operational and support meetings (Previous shift performance, discuss key constraints and risk and agree on the daily plan to enable operations to meet production target).
- Develop relationships with internal suppliers and customers, OEM, shared resource within the group.
- Monitor and evaluate action plans and targets for next week for the allocated department or section.
- Ensure new joiners adequately trained on the use of machinery, SOPs, policies and procedures, and company standards in their sections.
- Identify and report on nonconformances to company policies and procedures, guidelines and company standards within area or responsibility.
Safety, Health, and Environment
- Monitor and report on compliance to SHERQ regulations and system within area of responsibility.
- Ensure (Monthly quarterly, and annual) safety inspections are done and records kept.
- Facilitate the planning Internal & External audits (ISO9001; OHS Audit; Risk audit).
- Monitor time attendance (overtime, time worked, absenteeism) within area of responsibility and address problem areas with responsible heads of department.
- Review SHEQR indicators within area of responsibility and assist with addressing problem areas with responsible heads of department.
- Monitor and report on maintenance of process equipment.
Management of process
- Assist in the development of new product.
- Understand market, sale trends and which product range are fashionable.
- Understand product cost and impact of production.
- Understand what new technology and market trends are.
- Interpret daily/weekly targets from the monthly production plan and suggest improvements/solutions with problem areas.
- Ensure production outputs are according to specifications.
- Facilitate the departmental weekly KPI meeting, to review the previous weeks production.
- Appraise the department performance (including but not limited to safety; production stats; quality; top defects; waste and cost).
More jobs from Victoria Devereux International
-
HR and Labour Law Consultants
Johannesburg, South Africa - 3 weeks ago
-
HR and Labour Law Sales Consultant
Johannesburg, South Africa - 2 weeks ago
-
Deputy Factory Manager
Vereeniging, South Africa - 2 weeks ago
-
Senior Factory Manager
Vereeniging, South Africa - 2 weeks ago
-
Chief Financial Officer
Johannesburg, South Africa - 2 weeks ago
-
Chief Financial Officer
Vereeniging, South Africa - 2 weeks ago